Management of the maintenance department
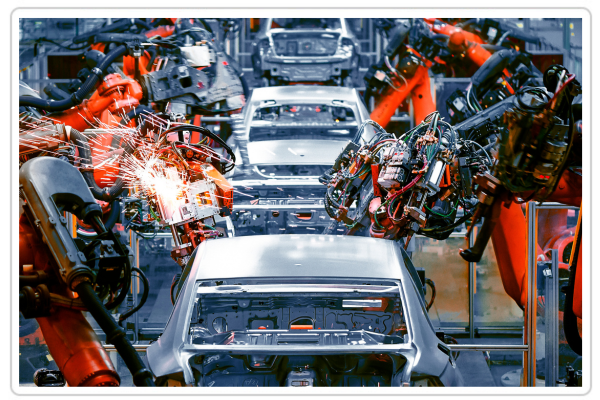
The main goal of the maintenance department is to ensure production continuity, improve machine efficiency and minimize failures and downtime. Such activities are necessary for the proper functioning of the enterprise. Effective management of machinery requires flexibility and adaptation of strategies to the changing conditions and needs of the production plant.
The tasks of this department include periodic maintenance of machines, aimed at extending the life of the device. In the event of a failure, technicians diagnose and repair the machine so that it returns to production as quickly as possible. In addition, the maintenance department manages inventories and spare parts for machines to be able to respond immediately if necessary. Each machine downtime generates costs because the production process stops. Therefore, it is extremely important to keep the devices in the best possible technical condition and to maintain a stock of parts so that they are at hand when needed. Additionally, thanks to proper parts warehouse management (Just In Time), you can also significantly save on warehouse space. Storing frequently unused components generates costs that can be avoided. For this purpose, it is determined which parts will be needed most often and which will be needed least. This is about improving production processes by improving efficiency and minimizing maintenance costs.
Maintenance department management strategies
To achieve the above-mentioned goals, manufacturing companies use various strategies to manage the maintenance department and parts warehouse. Here are a few of them:
Strategy of operating the machine until failure occurs. Run to Failure (RTF) is a thoughtful and deliberate action involving the operation of the machine until failure occurs. As long as a given machine is working, it does not require any additional actions. However, this strategy is used for less significant devices in the machinery fleet. This concept will also work when inspections and maintenance of machine parts do not reduce the likelihood of failure. Examples of such devices include lamps and screens, which can be easily, quickly and cheaply replaced or repaired. Some machines, in turn, can be very expensive to maintain, making regular inspections impossible in some companies. The procedure in the event of a failure is already thought out and carefully planned, including: who is responsible for repairing the device and what parts will be needed.
Maintenance based on the technical condition of the device called Condition-Based Maintenance (CBM). The strategy involves monitoring the technical condition of devices and, on this basis, a decision is made about a possible inspection or other preventive action. As a result of regular inspections, the risk of failure is reduced and the intervals between machine overhauls are extended. During device diagnostics, several factors are analyzed, e.g. the oil in a given machine is analyzed.
Preventive Maintenance (PM), which involves carrying out activities aimed at preventing failures. The strategy consists of regular machine inspections and preventive actions. In other words, actions are planned to prevent device failure and, consequently, avoid downtime. Such treatments include, among others: periodic inspections of the machine, maintenance planning and renovations, replacement of parts. Most often, software that enables machinery management is used for this purpose, because large amounts of data need to be analyzed and saved. All this to increase the efficiency of production processes, reduce the number of machine breakdowns and downtime, and reduce maintenance costs with the least amount of work.
Software supporting management and maintenance of machinery
The use of software supporting the management and maintenance of machinery is often necessary to maintain production flow. Depending on the type of system and the company's needs, it may consist of many functions. Select maintenance software allows you to plan inspections and maintenance of machines, monitor technical condition, manage parts and spare parts warehouses, report failures, assign technicians to specific departments and analyze collected data. Such activities allow for very accurate documentation, planning of purchases and production requirements, and disciplines the team of technicians. In the event of an internal or external audit, you can quickly and easily print the necessary report. The software significantly shortens the response time from reporting a failure to its repair, which affects the company's efficiency, reducing downtime and increasing the company's profit. The IT system also has a positive impact on the safety of the machinery and allows for greater control over devices. SmartMaint is specialized software supporting the work of the maintenance team and other departments of a manufacturing company. It enables production employees (operators and managers) to report faults and failures of the production line to the maintenance department. Thanks to the SmartMaint program, the maintenance team receives immediate notifications on their phones and starts working on fixing the failure. This tool allows you to direct recommendations to specific technicians and significantly shortens the response time to reported problems.
Contact us to learn more about SmartMaint and take advantage of a 14-day free trial! Write to us: bok@smartmaint.pl